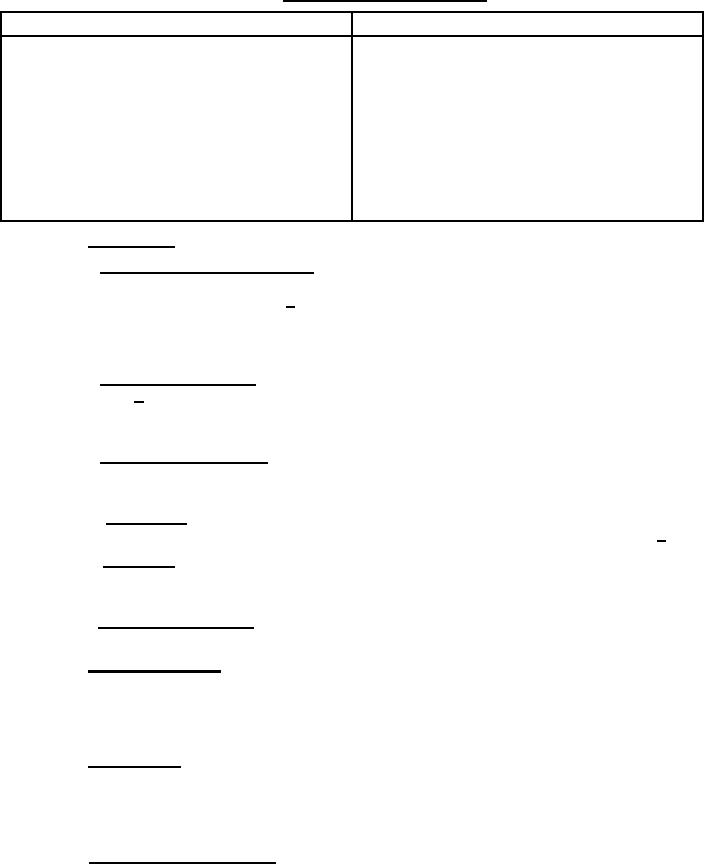
MIL-PRF-6085E
TABLE I. Properties of the finished oil.
Characteristic
Value
Viscosity in centistokes
at 54°C (min)
8
at -54°C (max)
12,000
Pour point (max)
-57°C
Flash point (min)
185°C
Precipitation number (max)
0
Acid number
report
3.4 Performance
3.4.1 Corrosion and oxidation stability. When tested as specified in section 4 the change in
weight of cadmium-plated steel, copper, steel aluminum alloy, and magnesium alloy, when subjected to
the action of the oil for 168 hours at 121°C +1°C, shall be not greater than 0.2 mg per square cm of
surface for each strip. There shall be no pitting, etching, or visible corrosion on the surface of any of the
metals when viewed under magnification of 20 diameters. Slight discoloration of the surface of the
copper will be permitted, but dark brown, gray or black stain shall be cause for rejection.
3.4.2 Resistance to oxidation. When tested as specified in section 4, the oil shall not have
changed more than +5 percent from the original viscosity in centistokes at 54.4°C after the oxidation-
corrosion test (see 4.4.2). The neutralization number increase shall be not greater than 0.5 after
oxidation. There shall be no evidence of separation of insoluble materials or gumming of the oil.
3.4.3 Low temperature stability. When tested as specified in section 4, there shall be no gelling
or separation of solid or liquid phases in the oil after storage at a temperature at or below -54°C for 72
hours. The presence of a dense cloud, which does not "settle out", shall not be the cause for rejection.
3.4.4 Evaporation. When tested as specified in section 4, there shall be not more than 1.80
percent by weight evaporation loss after the oil has been subjected to the test conditions, at 120°C +1°C.
3.4.5 Corrosivity. When subjected to the test specified in section 4, the test areas of the three
discs shall show no evidence of corrosion, pitting or other attack. The discs may show no more than
three spots within the area covered by the clip.
Color and appearance. When tested as specified in section 4, the oil shall be clear,
3.5
transparent and uniform in appearance, and not darker than No. 5 Union Colorimeter of ASTM D1500.
3.6 Protection of panels. When tested as specified in section 4, not more than one panel out of
five panels shall fail after being covered with a film of lubricating oil for 100 hours. If more than one panel
fails, the product shall be retested by repeating the same test with an additional ten panels. Not more
than four panels shall fail out of the total 15 panels, (the five panels on the original test plus the ten panels
on retest).
3.7 Workmanship. The oil shall be entirely homogeneous and free from lumps of undissolved
additive, water, dirt, lint or sediment. Prior to final packaging the oil shall be filtered through a 0.45
micrometer pore-size filter.
4.
VERIFICATION
4.1 Classification of inspections. The inspection requirements specified herein are classified as
follows:
a. Qualification inspection (see 4.2).
b. Periodic qualification re-evaluation (see 4.2.4).
4
For Parts Inquires call Parts Hangar, Inc (727) 493-0744
© Copyright 2015 Integrated Publishing, Inc.
A Service Disabled Veteran Owned Small Business