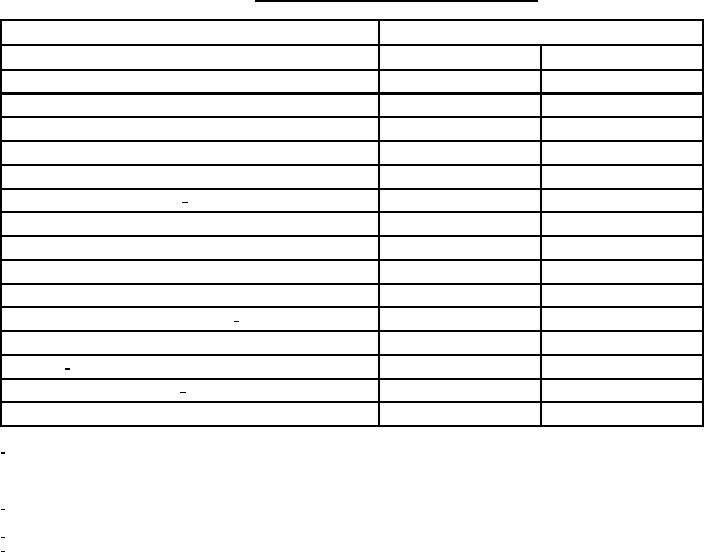
MIL-PRF-27601C
4.4.3 Compatibility. Samples of candidate fluid in amounts of 29 ml, 100 ml, and 180 ml shall be mixed with
samples from each of the fluids previously approved under this specification. Total volume of each mixture shall
be 200 ml. Mixtures shall be prepared in 250 ml stoppered flasks. The flasks shall be thoroughly agitated and
then stored in an oven at 135°C for 2 hours. At the end of this time, none of the mixtures shall show any sign of
sediment, turbidity, or crystallization. The samples shall then be stored at -54°C for a period of 2 hours. Slight
turbidity at this time, which later disappears, will be permitted in the samples.
4.4.4 Bulk modulus. Bulk modulus will be determined in accordance with 4.4.4 in MIL-PRF-87257.
TABLE VII. Test methods for hydraulic fluid properties.
Test Method
Characteristic
FED-STD-791
ASTM
Pour point
D 97
Flash point
D 92
Fire point
D 92
Specific gravity
D 1298
Viscosity
D 445
Solid particle contamination 1/
3009
Foaming
D 892
Water
D 1744
Neutralization number
D 664
High temperature-high pressure spray ignition
6052
Corrosiveness and oxidation stability 2/
D 4636
Low temperature stability
3458
Lubricity 3/
D 2532
Swelling of synthetic rubber 5/
3603
Flame propagation
D 5306
1/
Particulate contamination may also be measured by the use of automatic particle counters in lieu of the optical procedure detailed in
method 3009 of FED-STD-791. HiAc counter, Models PC-202, PC-203, PC-305, or equivalent, counting to the limits specified in table III.
Directions in the manual for the respective instruments shall be followed. A gravimetric determination shall also be made by ASTM D
4898.
2/
Bath, constant temperature, 175°C. Test time, 48 hours. Use metals as shown in figure 1. Substitute heptane or acetone as the solvent
material. Use hexane, heptane, and/or acetone to clean coupons. Use Alternate Procedure 2.
3/
A 10 ± 0.5 ml sample shall be used, and the test shall be conducted for 1 hour at each load specified in table V.
4/
Test at 204°C for 70 hours. Use standard FKM (see 3.3.14 and 6.4) within 6 months of date of manufacture.
4.4.5 Thermal stability. The thermal stability test shall be conducted in a 46 ml capacity stainless steel pressure
cylinder conforming to figure 1. Catalysts of each M-10 tool steel, 52100 steel and naval bronze shall be in the
form of 1.27 cm balls. The cylinder shall be charged with a 20 ml sample of the candidate hydraulic fluid, and the
catalysts placed in the cylinder. The system shall be purged with nitrogen, sealed at atmospheric pressure and the
test begun. The temperature shall be raised to 315°C and maintained for 22 hours. The nitrogen pressure is
5
approximately 1.38 X 10 Pa. Change in viscosity at 40°C, catalyst weight loss, and neutralization number shall
be reported
8