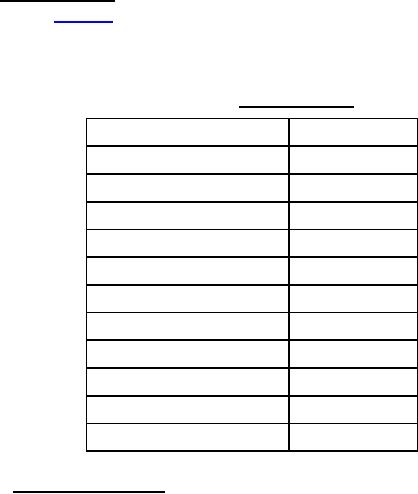
MIL-DTL-17111E
cost-effective sampling procedures to verify performance. Consult with the contracting official
for alternatives that replace verifications required by this specification.
4.5.3 Test procedures. The transmission oil tested in accordance with the applicable
methods specified in table IV. Physical and chemical values specified in section 3 apply to the
average of the determinations made on the samples for values which fall within any stated
repeatability of the applicable test method.
TABLE IV. Test procedures.
Test
Test document
Neutralization number
ASTM D974
Aniline point
ASTM D611
Precipitation number
ASTM D91
Viscosity
ASTM D445
Pour point
ASTM D97
Flash point and fire point
ASTM D92
Water
ASTM D95
Color
ASTM D1500
Shear stability
ASTM D5621
Steel-on-steel wear
ASTM D2266
Evaporation at 66 °C
ASTM D972
4.5.3.1 Aniline point change. Five milliliters (mL) of the petroleum base stock shall be
placed in a clean, dry Babcock cream test bottle having a capacity of approximately 50 mL with a
graduated neck, commonly known as the 9-inch, 9-gram, 50 percent X 1/2 cream bottle. The
standard 6-inch, 9-gram, 50 percent X 1/2 cream bottle may be used as an alternative. Then 20 mL
of 37 normal sulfuric acid shall be added cautiously but without delay to the test bottle in such a
way as to wash down any oil remaining in the neck of the bottle. The test bottle shall then be
shaken for at least 10 seconds, swinging the bottle through an arc of approximately 20 degrees so
that the bottom of the bottle passes through a distance of 2.5 inches to 3.5 inches. The speed of
shaking shall be maintained at 240 cycles to 300 cycles per minute. The temperature of the acid-oil
mixture shall not be allowed to approach 100 °C as indicated by the bottle becoming too warm to
touch. The bottle may be cooled in cold water if necessary. The bottle containing the acid-oil
mixture shall then be placed in a water bath maintained at 98 °C to 100 °C so that the liquid
contents are completely immersed. After the test bottle has been in the bath for 10 minutes, it shall
be removed and shaken in the manner described above for at least 10 seconds and replaced
immediately in the water bath at 98 °C to 100 °C. This procedure shall be repeated for a total of six
immersions and shakings except that the bottle shall not be replaced in the bath after the last
shaking. Sufficient 37 normal sulfuric acid shall be added to the contents of the test bottle to raise
the oil layer into the graduated neck. The bottle and contents shall then be placed in a centrifuge
and spun at a speed of approximately 500 revolutions per minute (rpm) for 10 minutes. The oil
8
For Parts Inquires call Parts Hangar, Inc (727) 493-0744
© Copyright 2015 Integrated Publishing, Inc.
A Service Disabled Veteran Owned Small Business