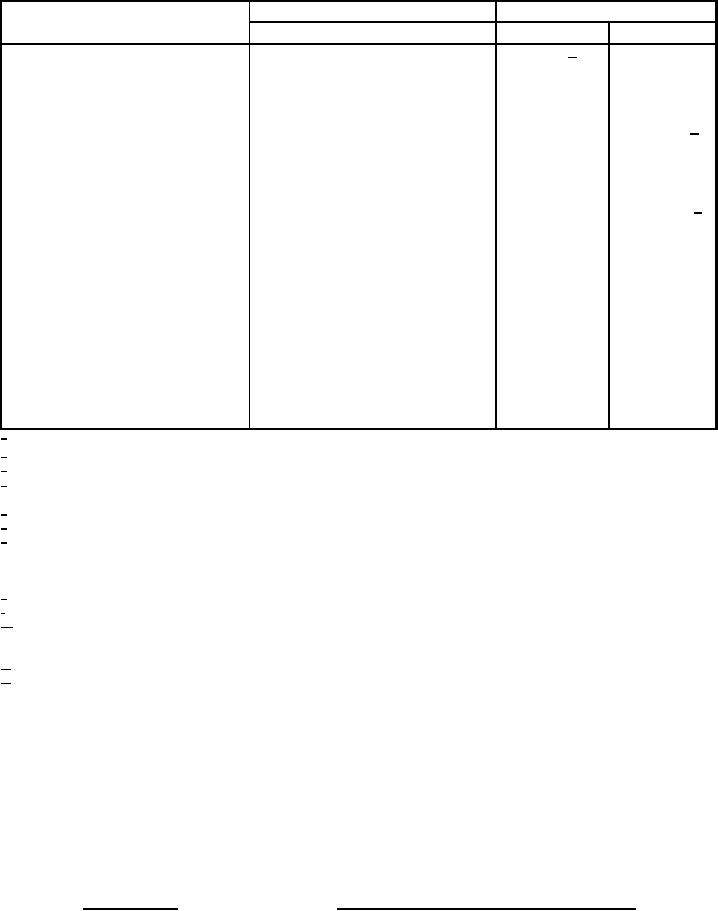
MIL-PRF-87100A(USAF)
TABLE I. Chemical, physical, and performance requirements. (cont)
Characteristic
Requirement
Test Method
ASTM
FED-STD-791
Specific heat at:
D276610/
260ºC(500ºF)
0.45 min
160ºC(320ºF)
0.40 min
60ºC(140ºF)
0.35 min
Compatibility
FTM 340311/
Turbidity
none
Sediment, ml/200 ml oil, maximum
0.005
MIL-PRF-87100
Corrosion and oxidation stability at
D4636
FTM 530712/
320ºC(608ºF)
-5 to +25 max
Viscosity change at 40°C, %
Acid number change,
0.20 max
mg KOH/g
2
Metal weight change, mg/cm
±0.2 max
Al
±0.2 max
Ag
±0.2 max
Fe
±0.2 max
M-50
±0.2 max
WSP
±0.2 max
Ti
1/
Titrate to a pH 11 end point.
2/
Viscometer shall be in accordance with ASTM D445. Test conditions will be specified by the activity responsible for qualification (see 6.3).
3/
Diluent shall be reagent grade.
4/
Use a 6 hour test period, ambient atmospheric pressure, and a bath temperature controlled within ±2ºC of test temperature. Air temperature
shall be maintained within ±2ºC of bath temperature, using a preheater if necessary.
5/
Report total ml sediment per 200 ml of oil instead of average ml sediment per 100 ml of oil.
6/
Use ASTM 114H-62 hydrometer.
7/
Report foam collapse period in seconds. Complete foam collapse is adjudged to be that point at which no more than a single row of bubbles
remain around the cylinder wall and the air inlet tube. If this ring of bubbles around the cylinder wall contains segments having two or more
layers of bubbles and the difference in height of the foam in the ring is not greater than 10 ml, complete foam collapse is adjudged to be that
point at which a break occurs in the ring of bubbles without subsequent reforming of the ring.
8/
Foam volume measurements taken after 5 minute aeration.
9/
See paragraph (4.4.2) for test method details.
10/
Values may be calculated from an equation of specific heat vs. temperature derived from minimum of five determinations of enthalpy
change made over the specificed temperature range. These shall include determinations of enthalpy change made at elevated
temperatures within ±20°C(±36° F) of each of the three required test temperatures.
11/
See paragraph (4.4.4) for test method details.
12/
See paragraph (4.4.5) for test method details.
3.4.2.2 Gear load-carrying capacity requirement conducted at 220ºC(428ºF). Load-carrying capacity shall be
determined in accordance with FED-STD-791, Method 6517, and the following test conditions:
AMS 6475* (Nitralloy N)
Gear Material
220±3ºC(428±5ºF)
Gear Temperature
205±3ºC(401±5ºF)
Test-oil-in-Temperature
74±3ºC(165±5ºF)
Support Oil-in Temperature
Only those gear machines with a reference oil "C" average rating (using AMS 6260 test gears) within the
range of 438 to 578 kN/m (2500 to 3300 lbf/in) are acceptable.
*
Gears shall be finished machined including gear tooth profile grinding after nitriding.
Load-Carrying Capacity
Avg % Relative Rating x 508 kN/m (2900 lbf/in)
Determinations
2 minimum
168 kN/m (960 lbf/in) min
6
For Parts Inquires call Parts Hangar, Inc (727) 493-0744
© Copyright 2015 Integrated Publishing, Inc.
A Service Disabled Veteran Owned Small Business