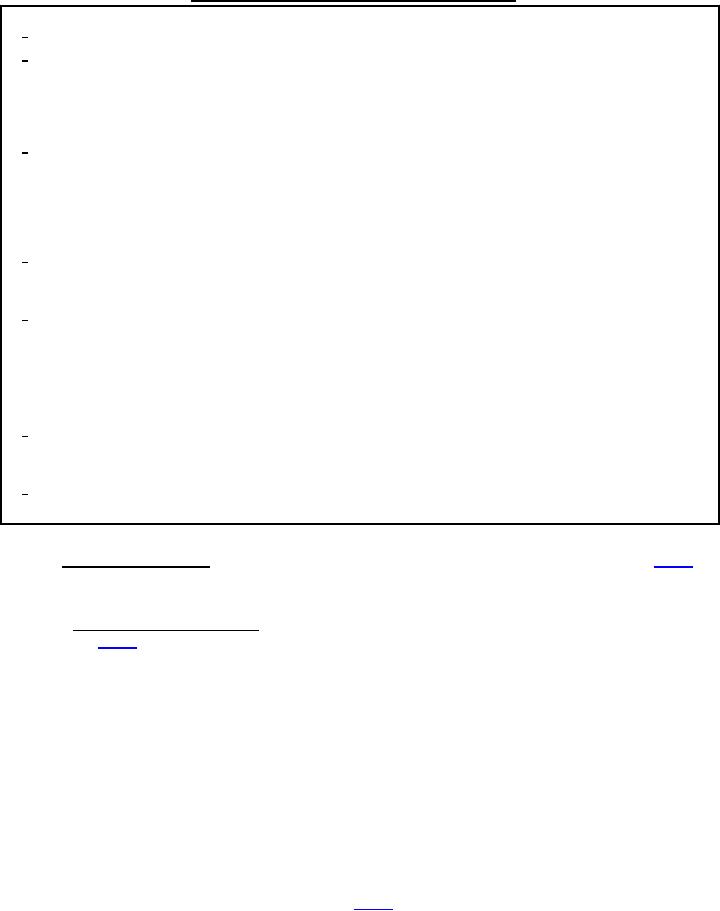
MIL-PRF-17331K(SH)
TABLE I. Chemical and physical requirements and test methods Continued.
NOTES:
1/
In conformance testing, values are compared to qualification results (see 4.3.1).
2/
Prior to the test, the oil shall be water-washed as follows: 300 grams of the oil to be tested shall be stirred
with 50 grams of water for 30 minutes at 90 °C (194 °F) using the beaker and stirrer as specified in ASTM
D665. After 30 minutes stirring, the mixture shall be transferred to a separatory funnel and left to separate.
Then the water layer shall be drawn off and the oil submitted to the salt-water corrosion test. The test shall be
run for 24 hours.
3/
Distilled water and stirring temperature of 54 °C (130 °F) shall be used. Discrete water droplets entrained in
the oil layer and clinging to the wall of the cylinder may be added to the water layer at a volume of 0.1 mL
per droplet. The results shall be reported using the format of oil layer/water layer/emulsion layer (time in
minutes). There is no requirement for water layer. The emulsion limit applies to any of the three types of
emulsions defined in the test method. If more than one emulsion type is present, the 3 mL maximum limit
applies to the combined volume of the different emulsion types.
4/
The total iron content shall be determined using the procedure and calculations described in the Procedure for
Determination of Sludge Weight and the Procedure for Determination of Copper in Oil, Water and Sludge for
Procedure A of ASTM D4310, except iron shall be substituted in place of copper where appropriate.
5/
Testing conditions shall be:
(a) Load: 15 kilograms
(b) Oil temperature: 80 °C
(c) Speed: 600 revolutions per minute (rpm)
(d) Duration of test: 120 minutes
6/
Option A is not allowed on freshly blended oils. If testing is done more than 1 week after blending, Option A
is allowed. A ring of bubbles around the edge of the graduated cylinder shall be considered complete
collapse or 0 mL.
7/
Sample shall be tested in accordance with ASTM D4898 using 0.8-micrometer pore diameter membrane
filters.
4.3 Conformance inspection. Each sample selected as specified in 4.3.2 shall be tested as specified in table I
and 4.4.6 except that the scuffing load capacity (FZG), oxidation test (ASTM D943), wear test, compatibility, air
release, and homogeneity tests will not be required.
4.3.1 Lot conformance requirements. The results from each sample selected as specified in 4.3.2, when tested
as specified in table I, shall not vary from the analysis of the sample given qualification approval by more than the
tolerances listed below:
a.
Gravity, degrees API: ±1.0
Sulfur, percent: ±20 percent of value for qualified product (1)
b.
c.
Viscosity:
(1) mm2/s kinematic at 4.4 °C (40 °F): maximum 870
(2) mm2/s kinematic at 40 °C (104 °F): ±8 (2)
(3) mm2/s kinematic at 100 °C (212 °F): ±1 (2)
Pour point, °C: ±3 (2)
d.
e.
Oxidation by rotating pressure vessel: -15 percent maximum
(1)
For oils qualified below 0.15 percent sulfur: no minimum restriction. Plus 0.08 percent allowable.
(2)
Shall meet requirements of this specification (see table I).
6
For Parts Inquires call Parts Hangar, Inc (727) 493-0744
© Copyright 2015 Integrated Publishing, Inc.
A Service Disabled Veteran Owned Small Business